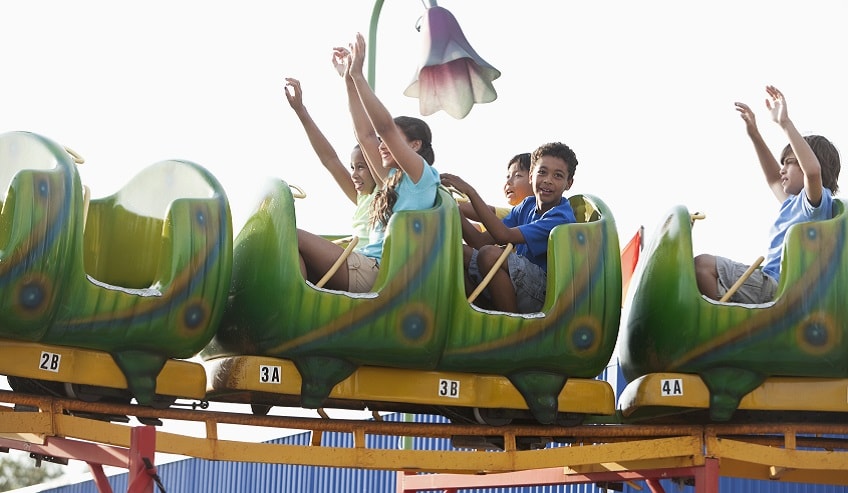
The Glue Talk Blog
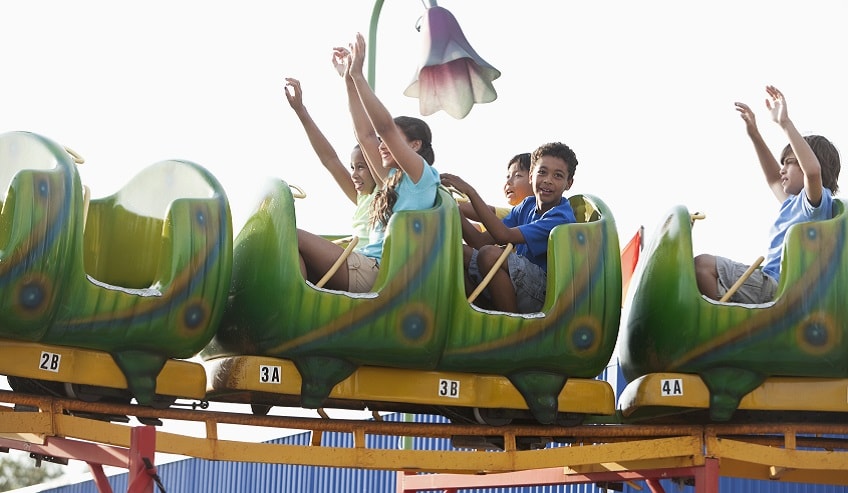
H.B. Fuller, with the acquisition of Royal Adhesives, introduces a new product to market: CILBOND®, designed to bond rubber to metal and polyurethane (PU) to substrate. Both are very difficult substrates to bond. Interestingly, this technology is used in the production of roller coasters, specifically the wheels.
A Brief History of Roller Coasters
Roller coaster history dates back to the 16th and 17th centuries when riders in Russia would enjoy shooting down the slope of ice slides. While this evolved into more complex rolling carts in France and elsewhere around the world, the first known roller coaster where the train was attached to the track was the Russes a Belleville in 1817.
The first American roller coaster was the Mauch Chunk Switchback Railway. It was built in the mid-1800s in the mountains of Pennsylvania and originally intended to send coal to a railway (but turned into a scenic tour). For the next few decades, scenic rides and wooden roller coasters became popular amusement park attractions, and despite a decline in production with the Great Depression and World Wars, a boom in the 1970s and 1980s revitalized the industry.
According to the International Association of Amusement Parks and Attractions, today there are an estimated 400+ amusement parks and attractions in the United States, and 300 more in Europe. Annual attendance is estimated to be 375 million guests in North America, 368 million guests in Asia Pacific, 161 million guests in Europe, the Middle East, and Africa, and 30 million guests in Latin America.
Roller Coaster Safety
Given that nearly a billion people visit amusement parks annually, safety is top of mind in roller coaster manufacturing and maintenance. Specifically on the roller coaster train that carries the passengers, the wheels are made from polyurethane (PU) bonded to a metal hub (usually aluminum or steel) and go through a hot casting process in which the PU is mixed, poured, and placed in a cure oven for an extended period of time. The hubs are coated with CILBOND® 49SF, a single-component bonding agent for hot-cure (>160°F/70°C) castable polyurethane elastomers and injection molded TPU systems, prior to being placed into the mold and before casting. During the curing process, the bonding agent is cured in parallel with the PU.
The bonding agent is a critical portion of the product design. Without it, the component would fall apart and disassemble. Given the high heat that can be generated during long runs of the coaster and especially during high-speed turns with forces on the wheel that stress the PU and bond, it’s imperative that the bonding agent can withstand extreme temperatures and dynamic fatigue performance requirements (the world’s fastest roller coaster is currently the Formula Rossa in United Arab Emirates, reaching speeds of 150 miles per hour).
Also, if the bonding agent fails, the ride would need to be shut down for maintenance. Thus, it is critical for customer satisfaction, revenue, and safety in the event the wheels fail and the coaster stalls on the track with people.
Learn more about CILBOND® high-performance one-coat bonding agents, and contact an H.B. Fuller expert today.
Blog Categories
Blog Categories
Archive
- 2024
- 2023
-
2022
- February (4)
- March (3)
- April (1)
- May (2)
- June (5)
-
August (6)
- Beverage Labeling Market In Africa: A Huge Potenial
- H.B. Fuller’s Glue House: Scavenger Hunt
- Increasing Global Aging Population: Impacts and Challenges
- Innovations and Key Challenges in Sustainable Disposable Absorbent Hygiene Products
- Supporting Racial Equity in Our Community
- Top 5 Reasons to Invest in H.B. Fuller
- September (4)
- November (2)
- December (2)
-
2021
- January (3)
-
February (7)
- Celebrating Exceptional Service During COVID-19 Complications
- Cyanoacrylates: What They Are and What They Do
- Innovative two-shot bookbinding adhesive
- Make a Difference 2020
- Problem Solving: Paper straws in drinking beverages
- Stronger straws
- Substances of Interest in Disposable Absorbent Hygiene Products
- March (4)
- April (4)
- May (4)
- June (5)
- July (2)
- August (5)
- September (2)
- October (1)
- November (3)
- December (2)
-
2020
- January (4)
- February (2)
- March (3)
- April (4)
- May (3)
-
June (7)
- Community Support in the Era of Coronavirus
- Employee Creates Face Shields with 3D Printer
- Improved Packaging Integrity and Greater Customer Satisfaction
- Liquid-Resistant Paper Straws
- What is a Sealant
- What Is the Future of Commercial Disinfectants
- Winning over consumers with e-commerce packaging solutions
-
July (6)
- Employees Take Action to be Part of Healing and Growth
- Gain a competitive advantage with packaging adhesive solutions
- HB Fuller Company Foundations Commitment to Communities
- Packaging Solutions for the South African Agriculture Market
- Supporting Organizations That Provide STEM Education for Youth
- Where Does Sustainability Stand Amid COVID-19
- August (3)
- September (2)
- October (4)
- November (2)
- December (4)